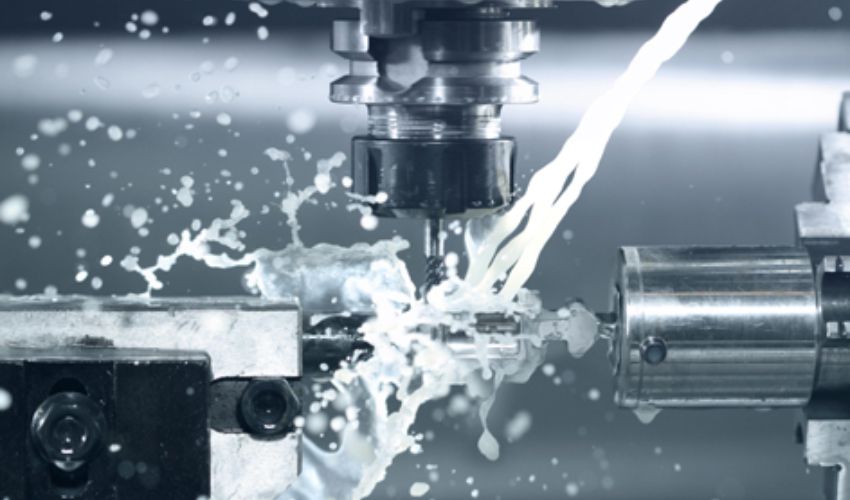
Introducción a los Fluidos de Corte
Los fluidos de corte juegan un rol muy importante para optimizar los procesos de operación en el trabajo de la industria metal mecánica, dentro de sus procesos de torneado, barrenado, maquinado, rectificado, troquelado, etc... Sus beneficios impactan directamente en la vida útil de las herramientas, velocidad y calidad del trabajo así como en la productividad de los equipos.
La función primaria de un fluido de corte es el control de la temperatura a través del enfriamiento y la lubricación, tanto de las piezas en proceso como de las herramientas de corte. Las propiedades de enfriamiento y lubricación de un fluido son críticas en el descenso del desgaste de las herramientas incrementando así vida útil.
Una función secundaria de los fluidos de corte es el ayudar a arrastrar con él las rebabas o virutas de metal, apartándolos de las herramientas y de las piezas en proceso, previniendo así terminados defectuosos de las partes y facilitando su manejo.
Los fluidos más comunes para el trabajo con los metales pertenecen a alguna de estas categorías:
- Fluidos base aceite, que incluyen aceites directos y aceites solubles.
- Fluidos químicos, que incluyen aceites sintéticos y semisintéticos.
Los aceites directos no son emulsificables, son utilizados en operaciones de maquinado sin ser diluidos en agua. Están compuestos de una base mineral o aceite de petróleo y comúnmente contienen lubricantes polares como son las grasas animales, aceites vegetales y ésteres, así como aditivos de extrema presión como el cloro, azufre y fósforos. Los aceites directos proveen la mejor lubricación y las peores características de enfriamiento entre los fluidos de corte.
Los fluidos sintéticos no contienen petróleo ni una base de aceite mineral y en su lugar están formulados con compuestos alcalinos inorgánicos y orgánicos junto con aditivos para inhibir la corrosión. Son generalmente utilizados en una forma diluida (Del 3 al 10 % de dilución en agua). Los fluidos sintéticos frecuentemente proveen el mejor desempeño de enfriamiento de entre los demás fluidos de corte, pero sus cualidades lubricantes son más pobres.
Los fluidos de corte solubles forman una emulsión cuando se mezclan con agua. El concentrado contiene una base de aceite mineral y emulsificantes que ayudan a producir una emulsión estable. Son utilizados en forma diluida (Del 3 al 10% de emulsión en agua) y proveen una buena lubricación y un buen desempeño en la transferencia de calor. Son los más utilizados en la industria y los menos costosos de entre los fluidos de corte.
Los fluidos semisintéticos son esencialmente la combinación de fluidos sintéticos y solubles con características comunes para ambos tipos. Este tipo logra la mejor relación entre enfriamiento y lubricación. Contiene también otros ingredientes como emulsificadores, inhibidores de corrosión, limpiadores, antiespumantes y bactericidas.
Manejo del Fluido de Corte
Se realizan análisis constantemente a los fluidos de corte solubles en agua ya mezclados y en operación, con el fin de reducir los costos de mantenimiento del fluido, mantenerlo en su mejor desempeño, lograr la mayor vida útil y tener consistencia en la alta vida de las herramientas y la calidad de las partes fabricadas, evitando la contaminación y degradación. Las empresas corren diferentes programas de mantenimiento, todos concentrados en monitorear propiedades particulares del fluido y la adición adecuada de químicos para mantener adecuadamente los parámetros del fluido en los límites propuestos. Los parámetros más importantes que son monitoreados para mantener la habilidad de desempeño de los fluidos en el maquinado son:
- La Concentración
- Nivel de PH
- Contaminación Bacterial
Concentración:
Es el porcentaje de la concentración de fluido de corte en la mezcla. La concentración puede expresarse también en proporción, es decir, la cantidad concentrada de fluido de corte que contiene el volumen total de la mezcla. Por ejemplo, agregar 4 litros de concentrado a 96 litros de agua equivale a 4% o lo que es lo mismo 1 a 25. Para obtener el máximo de los fluidos de corte debe ser utilizada la concentración recomendada en los parámetros de operación de cada equipo. Si la mezcla es muy rica o muy fuerte pueden presentarse varios problemas como espuma o acumulación de residuos, si la mezcla es muy suave o pobre pueden presentarse problemas de desgaste prematuro de las herramientas, rancidez, corrosión, oxidación prematura del producto terminado.
La concentración se determina por varios métodos: Por un refractómetro, Titulación Química, cintas de prueba o algunas pruebas más en laboratorio. La más fácil y práctica es la del refractómetro, su precisión es satisfactoria; para una lectura más precisa se recomiendan otras técnicas.
Nivel de PH:
PH es la medida de acidez o alcalinidad de la mezcla del fluido de corte, y es un importante indicador de la condición del fluido. Cada producto tiene un rango de pH especificado en el que opera con mayor eficiencia. La mayoría de los fluidos de corte operan en un rango de pH entre 8.5 y 9.2, aunque algunos sintéticos recientes pueden trabajar con eficiencia hasta en 7.5. Una mezcla con pH (menor a 8) bajo puede provocar rancidez, corrosión ferrosa e inestabilidad de la mezcla. Favorece el desarrollo de bacteria. Una mezcla con pH elevado (mayor a 9.5), por otro lado, incrementa riesgo de dermatitis e irritaciones en la piel, afectará la corrosividad del fluido y el control de la corrosión de metales no ferrosos, por ello es indispensable mantener la mezcla en el rango de pH recomendado por el fabricante, para evitar estos y otros problemas severos. Tomando la lectura a 25°C, un pH igual a 7 es neutro, menor que 7 es ácido y mayor que 7 es básico o alcalino. A distintas temperaturas, el valor de pH neutro puede variar debido al constante de equilibrio del agua. El valor del pH se puede medir de forma precisa mediante un potenciómetro, también se puede medir de forma aproximada empleando indicadores, ácidos o bases débiles que presentan diferente color según el pH, como la Fenolftaleína. Generalmente se emplea papel indicador, que se trata de papel impregnado de una mezcla de indicadores.
Contaminación Bacterial:
La contaminación bacterial de un fluido de corte puede ser determinada por un análisis de Cuenta de Bacteria. Es la medida de bacteria total en la mezcla del fluido de corte. Una cuenta de bacteria alta se manifiesta con malos olores y fallos en el desempeño. Existen varios métodos simples y accesibles para la determinación de la bacteria. La mayor parte de los fluidos para corte toleran una cuenta de bacteria de hasta 100,000 por ml. El análisis de oxígeno disuelto es también una buena medida de la actividad biológica.
Además de la revisión constante de la concentración de la emulsión, el PH y la revisión del crecimiento de bacterias, es necesario revisar el fluido por contaminaciones de aceites externos, como el aceite hidráulico utilizado en equipos, u algún otro aceite. Las acciones para mantener el fluido podrán ser: añadir fluido de corte, agua, desnatar los otros aceites, añadir bactericidas, filtrar residuos (virutas) o centrifugar.
El fluido de corte en el sistema se irá degradando debido a la formación de bacterias y contaminación externa (aceites y residuos metálicos). Cuando su desempeño se reduce y los costos de mantenimiento del fluido se incrementan, es necesario desecharlo. Antes de ser enviado al drenaje (revisar normas para cada entidad), es necesario tratarlo para que la composición del fluido cumpla los niveles seguros de desechos.
Otras pruebas que deben realizarse periódicamente a los fluidos de corte son:
Pruebas de Inhibición de Corrosión: Las propiedades anticorrosivas de los fluidos de corte son muy importantes para la protección de las partes metálicas que están en contacto con el fluido. Además, como la protección anticorrosiva de los fluidos de corte va disminuyendo significativamente al ser disuelto el aceite en agua, este es un buen indicador para añadir aceite al sistema. Las pruebas de corrosión están estandarizadas en DIN 51360 1 y 2.
Volumen de Sólidos o Lodos: Se refiere al porcentaje de sólidos en la mezcla del fluido de corte que se separa de la mezcla después de asentarse o centrifugarse. Los valores del lodo o sólidos deben ser menores a 0.1% del volumen. Altos valores de sólidos usualmente indican una filtración inadecuada del fluido o problemas con el filtro. Un alto contenido de sólidosdegrada el desempeño del fluido de corte y conlleva a problemas de residuos, terminados defectuosos, afecta la vida útil de los filos y favorece el crecimiento de la bacteria.
Aceite o Aceite libre: Es el porcentaje de aceite o material similar que no se encuentra emulsionado y que flota en la superficie de la mezcla del fluido de corte. Generalmente son fluidos hidráulicos o aceites de otro origen que se fugan hacia la mezcla. Su concentración no debe ser mayor al 0.5%. Si fuera mayor, puede hacer inestable la mezcla.
Aceite Total: Es el porcentaje de aceite o materiales similares presentes en la mezcla del fluido de corte. Incluye todos los aceites, los incluidos en el aceite de corte soluble y los ajenos.
Aceites Extraños o Ajenos: Es el porcentaje de aceite o materiales similares en la mezcla que no proviene del concentrad de fluido de corte. El aceite total en la mezcla se determina en laboratorio al separar la mezcla con ácidos en una prueba específica. Un alto contenido de aceite ajeno promueve problemas como los residuos, un pobre desempeño y el crecimiento de bacteria. Valores negativos de aceite ajeno (-0.5%) indican inestabilidad o contaminación de la mezcla.
Alcalinidad Total: Es la medida de los materiales alcalinos, tanto orgánicos como inorgánicos que se encuentran en la mezcla del fluido de corte. Una alcalinidad total arriba de lo normal promueve una mezcla irritante para la piel, causa corrosión de los materiales no ferrosos y otros problemas. La alcalinidad habitualmente incrementa mientras los equipos envejecen.
Conductividad: Es una medida de conducción eléctrica de un fluido de corte. Se expresa en mili Siemens por centímetro (ms/cm). Al incrementar los materiales disueltos en la mezcla del fluido (calcio, magnesio, sodio o cloro), la conductividad del fluido se incrementa. La conductividad se incrementa lentamente con el paso del tiempo, y la tasa de incremento depende también de la calidad y cantidad de agua, así como los tipos y concentraciones de otros contaminantes. Altos niveles de conductividad promueve problemas como los residuos insolubles, inestabilidad de la mezcla y reducción del desempeño. La inestabilidad de la emulsión ocurre habitualmente cuando la conductividad alcanza el rango de 4 a 5 ms/cm.
Cuenta Fúngica: Mide el hongo en la mezcla del fluido de corte. Una alta concentración de hongos causa malos olores, taponamiento de las líneas del fluido, y la falla del mismo. A diferencia de los análisis de bacterias en la que la cuenta se correlaciona con el crecimiento de la bacteria en el sistema, la cuenta fúngica no cuantifica acertadamente el hongo presente en o alrededor del sistema. El hongo es más probable que se aferre a las superficies y por ello puede estar muy presente en un sistema sin ser detectado en el análisis de una pequeña muestra.
ProCut10X – Fluido para Corte Soluble http://www.proktive.com/products/procut10x
ProTap10X – Aceite para Corte Directo http://www.proktive.com/products/protap10x
Más información, asesoría, servicio y apoyo con el seguimiento de sus aplicaciones contáctenos gerenciatecnica@proktive.com